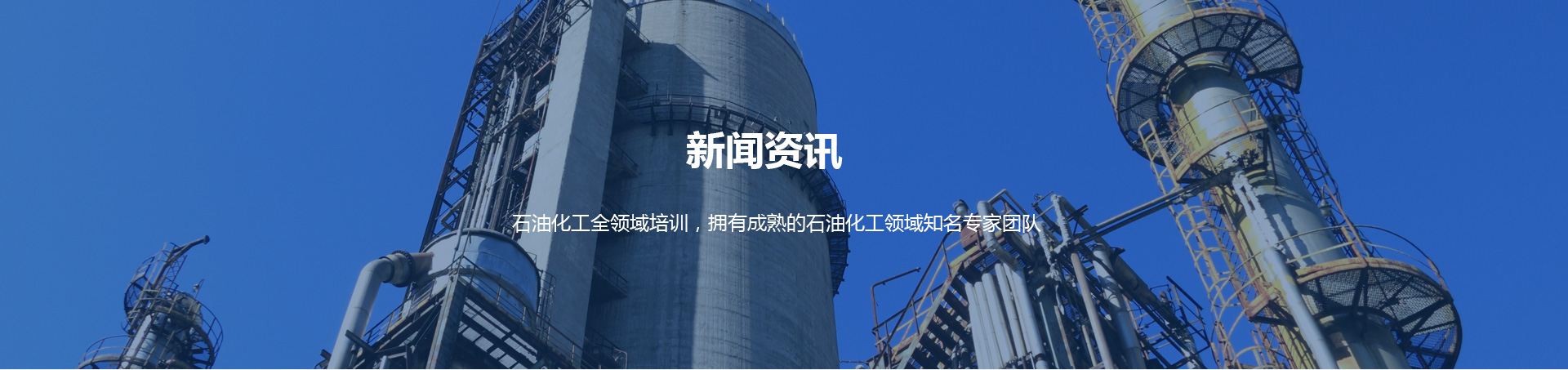
8月3日14时50分,兰州石化长庆乙烷制乙烯项目80万吨/年乙烯装置生产出合格乙烯产品。
这标志着国内首套利用中国石油自主研发技术建成的大型乙烯生产装置投料开车一次成功。
该项目是国内第一套利用中国石油自主研发的乙烷裂解制乙烯技术建成的大型乙烯生产装置,利用长庆油田天然气中分离出来的乙烷组份加工乙烯,较传统石脑油加工乙烯技术,具有工艺流程短、占地面积小、装置投资少、乙烯收率高、生产成本低等诸多优势,对优化利用天然气资源、提升国内乙烯生产技术水平,推动乙烯产业高质量发展,实现上下游一体化、大型关键装备“乙烯三机”和DCS控制系统国产化,贯彻“中国制造2025”战略具有重大引领和示范意义。
兰州石化公司长庆乙烷制乙烯项目是中国石油落实减油增化、实现转型升级的重点工程,也是中国石油“十四五”时期建成投产的第一套大型炼化项目。项目瞄准国际先进水平,对标世界一流企业先进指标,突破了传统乙烯生产能耗物耗高、乙烯收率低的制约,乙烯收率可由裂解石脑油的30%左右提高到80%,综合能耗降低到398.7千克标油/吨的世界先进技经指标,为我国乙烯产业从赶超到引领世界的角色转变发挥示范带动作用。
长庆乙烷制乙烯项目总投资约百亿元,以长庆油田天然气中分离的乙烷为原料,通过蒸汽热裂解生产乙烯、氢气、液化烃类气体混合物、燃料油等化工产品,并通过聚合反应生产聚乙烯产品。项目由80万吨/年乙烯装置、40万吨/年全密度聚乙烯(FDPE)装置、40万吨/年高密度聚乙烯(HDPE)装置和3万吨/年丁烯-1/己烯-1装置组成,是首批国家级示范工程、陕西省十大重点工程、兰州石化和集团公司炼化转型升级重点项目,乙烯装置工艺包技术采用寰球公司自主开发的“大型乙烯装置工业化成套工艺技术”。
寰球公司自主乙烷制乙烯工艺技术具有流程简洁、投资低和操作灵活的特点,乙烷裂解炉清焦周期和装置能耗等关键指标达到国际先进水平。在国家将“做好碳达峰、碳中和工作”列为重点任务之际,公司乙烯技术团队积极探索,优化工艺方案,先后完成了一系列技术创新:
一是开发裂解炉烟气脱硝系统,以满足裂解炉NOx排放环保要求;
二是开发裂解炉原料增湿塔配汽技术,成功降低装置能耗;
三是开发“气浮+聚结”的净化处理技术,提升急冷水质量;
四是根据原料轻质特点,深冷系统进行了冷量优化;
五是开发前脱乙烷前加氢分离流程,降低热泵操作能耗,实现节能减排和降本增效。
整个项目突出绿色低碳,采用了新型烟气脱硝、催化氧化处理废碱、超滤+反渗透及蒸发结晶等世界前沿新技术,实现二氧化碳、氮氧化物等废气超低排入。
裂解炉装置采用新型烟气脱硝技术,使氮氧化物排放比常规裂解炉装置排放降低70%,实现废气超低排放。
采用催化氧化处理废碱、超滤+反渗透及蒸发结晶新技术,实现废水深度回用,回用率达到95%以上,成为中国石油首家废水近零排放的炼化项目。
项目投用后二氧化碳排放量约34.24万吨/年,年综合能耗消耗量为75.52万吨标煤(不含乙烷原料),达到世界先进水平。
成为中国石油首家废水排放近零的化工项目,为推动我国“碳达峰”“碳中和”目标做出贡献。长庆乙烷制乙烯项目充分运用大数据、云计算等先进信息技术,融合通信、移动平台优势,成为集生产调度、机电仪管控、应急指挥一体的“智能化工厂”。
公司地址:北京市海淀区永泰园14号楼25层
邮箱:zzwygongsi@163.com
网址:www.bjzzwy.com
扫一扫关注我们